A common saying suggests “you can never have too much of a good thing”, but this is not true when it comes to supplying electricity. In fact, oversupplying electricity to a particular district can lead to enormous wastage.
Unlike money, excess electricity is not easily stored in wallets and banks. To ensure grid stability, unused electricity is often unloaded into the ground and subsequently lost.
According to data produced by GE Digital, the energy industry can save more than US$1 trillion worth of electricity and other financial benefits simply by better matching electricity supply to demand, through the use of digital power solutions.
That is, the process of using thousands of sensors to collect data across homes and factories. Complex digital analytics are then used to understand the data, and inform engineers where instances of electricity undersupply, and oversupply, are taking place. Power plants can also adjust supply ahead of time, based on user patterns and demographic trends.
According to Luis Gonzalez, chief digital officer for Asia Pacific, GE Power Digital Solutions, many power producers today purchase power based on economic forecasts, and not actual consumption. “Sometimes, there’s oversupply for the next 20 years because they’re being cautious, or undersupply because there’s no budget,” he shares with Eco-Business in a recent interview.
A community that sees a population growth of 20 percent, for example, could see its energy demand grow by more than 20 percent due to changing energy consumption habits, leading to an undersupply. Thus, live data is needed to meet electricity demand accurately, and do better predictions on the investment and performance required from power assets says Gonzalez.
Benefits to the environment
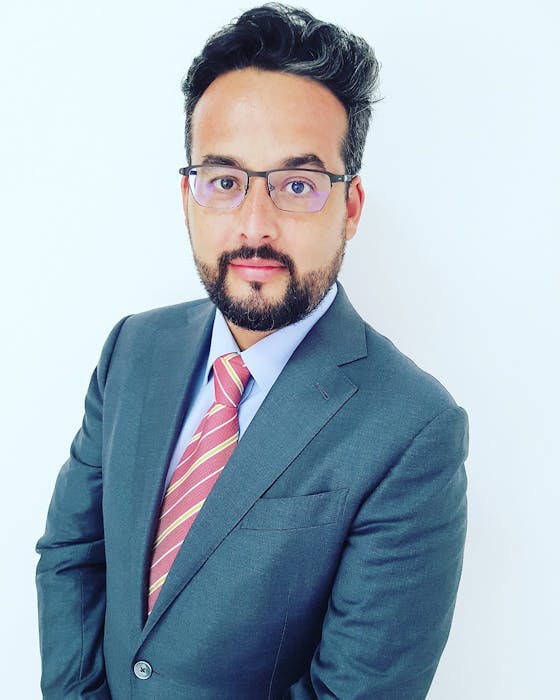
Luis Gonzalez, chief digital officer for Asia Pacific, GE Power Digital Solutions. Image: GE
The environment stands to benefit from efficient energy use. In a coal-fired power plant, digitally-enhanced efficiency could monitor and reduce emissions by up to three per cent. Should digital power be implemented on a global scale, GE Digital estimates that as much as 5.8 billion metric tons of carbon dioxide emissions could be avoided just by enabling fuel analysis and better combustion performance.
Digital power solutions can also be applied to both “big power” and “small power” projects.
“Big power” refers to large centralised power plants or integrated networks that supply power to huge grids. Data points – places where sensors can collect data – can be strategically installed at these places to gather information on a mass scale.
For instance, analysing data across 16 power plants and 1,400 miles of transmission lines for the New York Power Authority can generate up to US$2 billion of savings for this public network. These savings stem from more accurately matching supply to demand, using data analytics.
More commonly found in Southeast Asia, a region known for its vast archipelago, are “small power” facilities that provide off-grid electricity to rural communities on remote islands. Many of these growing island communities rely on diesel generators to produce electricity, despite the fact that such methods can be polluting.
Incorporating renewables into the energy mix can help provide cleaner power for these rural communities. Gonzalez says digital power solutions can play a part in managing their “power mix” – the proportion of conventional and clean power used – to stabilise power supply during disruptions.
GE Digital is implementing digital power technologies in some of its projects within Southeast Asia. This includes the Renewable Energy Integration Demonstrator in Singapore, and projects to implement fast and reliable power to rural villages in Indonesia.
Opportunities for digital “small power” facilities are set to grow. By 2020, GE Digital estimates that distributed power capacity additions will grow to 200GW, from 142GW in 2012. In addition, some 125 million people in Southeast Asia lack access to modern energy services and would stand to benefit from digital “small power”.
Changing mindsets
Despite the benefits of digital power, fear of job losses to the artificial intelligence technology it employs, and entrenched mindsets are among some reasons slowing down its global adoption, notes Gonzalez.
“Plant operators believe that the software is going to take away their jobs,” he explains. “What they’re not understanding is that it’s not really a matter of taking away their jobs. It’s a matter of making their jobs a little different.”
Industry, and energy users, need time to better understand the digital power concept, and how new solutions can transform operations, says Gonzalez. “Customers don’t quite understand what digital power will do for them. They haven’t allocated budgets towards it, and they’re still educating their board of directors, and themselves.”
Companies are also still in the process of shifting to a more collaborative data-sharing culture, adds Gonzalez. Shared data is needed for digital applications that allow power executives to observe a power plant, and system, in its entirety, he says. This allows power executives to adjust demand, and supply, across the whole system.
The industry lacks Chief information officers (CIOs) who are championing digital power, and where there are CIOs, “they tend to not have a strategic view in technology when it comes to software,” says Gonzalez. “The easier it is for them to understand what data collaboration is, the faster the change goes.”
But ultimately, the most challenging part of implementing digital power in a grid “has nothing to do with technology,” Gonzalez notes.
He adds: “It had to do with the ability of the plant to update their processes, and update their organisation to be able to handle it.”
Using the analogy of the self-driving car, Gonzalez explains that although autonomous vehicles can be made operational quickly, whether the operator could adapt as rapidly to the new procedures is a different story.
The key to success for customers is to develop their organizational digital competency to understand what the new technologies can do and match it with the right leadership, vision and governance to successfully extract value from these investments. A culture of innovation needs to be instituted to succeed with digital.
“
Plant operators believe that the software is going to take away their jobs. What they’re not understanding is that it’s not really a matter of taking away their jobs. It’s a matter of making their jobs a little different.
Luis Gonzalez, Chief digital officer for Asia Pacific, GE Power Digital Solutions
Improving safety and productivity
Beyond energy savings, digital power has the potential to boost innovation and safety, shares Gonzalez.
By using software to collect data, plant workers are spared from the time-consuming, and sometimes dangerous, process of manually monitoring the plant’s performance.
For example, data collected by software can help workers detect false power outages – instances where power was mistakenly thought to be cut. This prevents unnecessary and risky repairs, Gonzalez shares. Software data can also help determine the nature of the outage, allowing plants to deploy the right materials and personnel to fix the problem.
The time freed could be used to think about innovations that could further improve power generation. According to Gonzalez, digitally powered plants across Asia have experienced a 35 per cent decrease in the number of hours needed to run a plant, over five years.
As a result, workers have been able to go home earlier, to do more planning and figure out new ways to improve the plant.
Gonzalez says: “It becomes a virtuous cycle. The more time you have to think of improvements, the more these improvements get implemented, transforming operators into optimisers.”